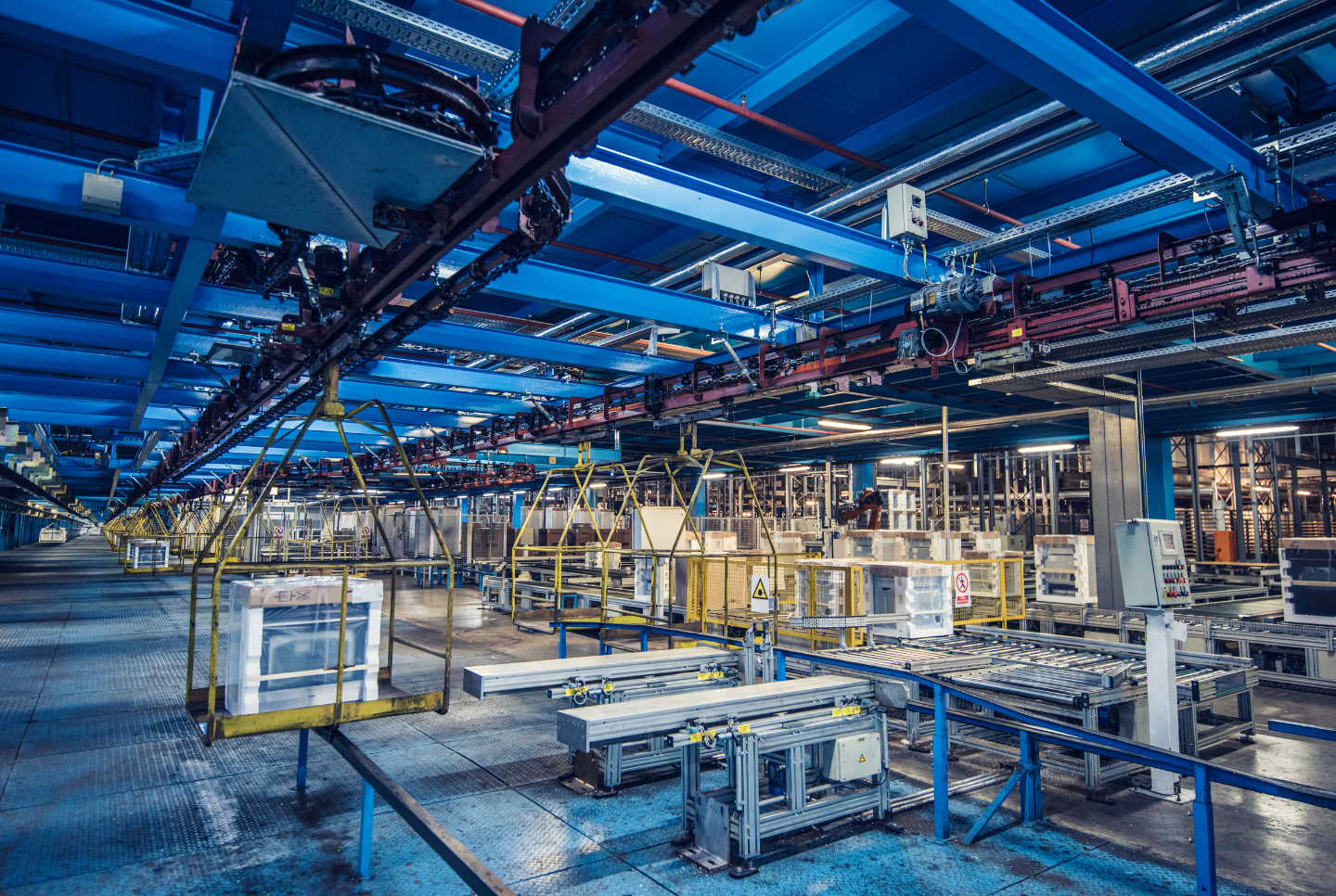
Every freight move relies on one thing: data.
But when that data is scattered across systems, spreadsheets, and emails, keeping operations running smoothly becomes an uphill battle. Instead of making quick, informed decisions, teams are stuck chasing information, fixing errors, and working around system gaps. The result? Higher costs, slower shipments, and frustrated customers.
For shippers, a disconnected supply chain is a direct threat to profitability. Without real-time data, teams struggle to track shipments, respond to disruptions, and control costs. Small inefficiencies compound over time, leading to missed deadlines, lost revenue, and higher operational expenses.
What a Connected Supply Chain Looks Like
A connected supply chain makes sure the right data reaches the right systems and teams at the right time. Instead of piecing together information from emails, spreadsheets, and siloed platforms, teams have a single, real-time view of their supply chain. This level of connectivity transforms operations, reduces costs, and enables faster, smarter decision-making.
Centralized Access to Supply Chain Data
Data is only useful if it’s accessible. In a connected supply chain, information from ERP, TMS, WMS, and data warehouses is seamlessly integrated, eliminating blind spots. Whether it’s tracking inventory, monitoring shipments, or managing compliance, teams no longer have to dig through multiple systems to find what they need. Everything is in one place, ready to power decision-making.
Real-Time Insights for Faster, Smarter Decisions
When disruptions happen, timing is everything. A connected supply chain provides live updates on shipments, inventory levels, and potential risks. Instead of waiting for reports or manually checking systems, teams get instant alerts and actionable insights. With real-time visibility, companies can respond to delays, optimize routes, and adjust inventory before small issues become costly problems.
Automated Workflows That Replace Manual Tasks
Manual data entry, reconciliation, and approvals slow everything down. A connected supply chain automates these tasks, reducing errors and freeing up teams to focus on higher-value work. Instead of chasing missing shipment updates or manually processing invoices, workflows handle these tasks in the background—ensuring data accuracy, speeding up operations, and cutting unnecessary costs.
Improved Collaboration Across Stakeholders
Supply chains involve multiple players—suppliers, carriers, customers, and internal teams. When systems aren’t connected, communication gaps lead to misalignment, delays, and costly mistakes. A connected supply chain ensures that everyone has access to the same, up-to-date information. Whether it’s coordinating handoffs between warehouses and carriers or keeping customers informed, better data sharing leads to smoother operations and stronger relationships.
Key Areas Where Supply Chain Connectivity Drives Cost Savings
When systems communicate automatically, teams can work faster, reduce errors, and make better decisions. Here’s where connectivity has the biggest impact on your bottom line:
Faster, More Efficient Freight Operations
Disconnected systems slow everything down. A connected supply chain speeds up freight operations by eliminating manual data entry, improving routing decisions, and optimizing capacity.
- Automated data flows reduce time spent tracking shipments, eliminating the need for constant status updates via email or phone.
- Integrated systems help teams select the best carriers and routes, cutting transportation costs and reducing delays.
- Better demand forecasting minimizes wasted capacity by ensuring the right amount of freight moves at the right time.
Risk & Compliance Management
Compliance failures and delays come at a high cost. A connected supply chain reduces these risks by automating regulatory processes and ensuring faster access to critical documentation.
- Automated regulatory checks help avoid fines and penalties by flagging compliance risks before they become issues.
- Instant access to documentation speeds up audits and customs clearance, reducing shipment delays and storage fees.
- Real-time tracking ensures teams can respond quickly to disruptions, avoiding penalties for late deliveries.
Lower IT & Operational Costs
Maintaining a patchwork of disconnected systems is expensive. A centralized connectivity solution reduces IT complexity, improves data management, and lowers overall operational costs.
- Less reliance on manual data processing reduces labor costs and eliminates human errors that lead to expensive rework.
- Fewer system integration headaches mean IT teams spend less time managing connectivity issues and more time on strategic initiatives.
- Improved data accessibility enables teams to allocate resources more efficiently, cutting unnecessary expenses.
Improved Supplier & Partner Collaboration
Supply chains depend on seamless coordination between LSPs, shippers, and third-party providers. Connectivity strengthens these relationships by improving communication and reducing errors.
- Faster communication between partners eliminates costly misalignment in shipment coordination.
- Shared visibility into order status and inventory levels enables proactive problem-solving, preventing disruptions.
- Seamless integration ensures that data flows smoothly between all stakeholders, reducing duplicate efforts and delays.
Real-Time Decision Making to Reduce Costs
A connected supply chain provides the data teams need to make proactive, cost-saving decisions. Whether it’s adjusting to market shifts or optimizing contracts, real-time insights drive better financial outcomes.
- Predictive analytics help resolve issues before they escalate, reducing costs associated with delays and disruptions.
- Data-driven contract negotiations with suppliers and carriers lead to better pricing and service agreements.
- Optimized inventory and warehouse management ensures that stock levels align with demand, cutting excess storage costs.
5 Steps to Build a Cost-Optimized, Connected Supply Chain
A connected supply chain doesn’t happen overnight. It requires a strategic approach to integrating systems, automating processes, and continuously optimizing for efficiency. Here’s how to get started:
Step 1: Assess Your Current Tech Stack and Identify Data Silos
Before making improvements, you need to understand where inefficiencies exist. Take inventory of your current systems and identify where data is fragmented.
- Which platforms do different teams rely on (ERP, TMS, WMS, spreadsheets, custom databases)?
- Where does manual data entry slow down operations?
- What key information is missing or hard to access?
Mapping these gaps will highlight where connectivity can create the most impact.
Step 2: Map Out Critical Integration Points
Once you’ve identified silos, determine how your core systems should communicate. Focus on integrating the platforms that drive daily operations:
- Enterprise Resource Planning (ERP) – Central hub for financials and supply chain planning
- Transportation Management System (TMS) – Manages freight movement and carrier selection
- Warehouse Management System (WMS) – Tracks inventory and fulfillment
- Third-Party Data Providers – Customs, compliance, carrier visibility, and analytics
A well-integrated system ensures that every team has access to the data they need—without relying on slow, manual workarounds.
Step 3: Automate Data Exchanges to Eliminate Manual Processes
Manual data entry and reconciliation waste time and introduce errors. Automating these workflows speeds up operations and reduces costs.
- Automate freight tracking updates instead of relying on emails and spreadsheets.
- Replace manual compliance checks with automated regulatory validation.
- Enable real-time inventory updates to improve order fulfillment accuracy.
Automation keeps data flowing without human bottlenecks, improving efficiency across the supply chain.
Step 4: Leverage a Supply Chain Connectivity Platform (Like Chain.io)
Rather than custom-building integrations between every system, use a supply chain connectivity platform to unify data exchange. Platforms like Chain.io simplify:
- System interoperability – Seamlessly connecting ERP, TMS, WMS, and external data sources
- Real-time visibility – Providing a centralized view of supply chain movements
- Scalability – Enabling fast adoption of new technologies without costly development work
A purpose-built connectivity platform eliminates the complexity of integrating disparate systems, allowing teams to focus on execution.
Step 5: Monitor and Optimize—Use Data-Driven Insights to Refine Operations
Supply chain optimization isn’t a one-time project—it’s an ongoing process. Once your systems are connected, use real-time insights to make continuous improvements.
- Analyze cost trends to identify savings opportunities.
- Monitor carrier performance and optimize freight routes.
- Track compliance metrics to avoid unnecessary penalties.
Succeed with Connected Supply Chain Data
A connected supply chain is the foundation for reducing costs and improving efficiency. By unifying your data across systems, automating processes, and enabling real-time insights, you can streamline operations, improve decision-making, and ensure greater collaboration. Whether you’re optimizing freight movement, managing risk, or enhancing supplier relationships, connectivity is key to unlocking significant cost savings and operational improvements.
To start, assess your current supply chain and identify where gaps exist in your data flow. These gaps are opportunities for improvement, and addressing them will lead to smoother, more efficient operations.
At Chain.io, we move the data that moves your freight. Our platform drives cost optimization for logistics service providers and shippers by connecting your business to other businesses and applications, giving you control over the data you need to manage your supply chain. Our pre-build connectors let you build a connected supply chain quickly, so you can get out of project meetings and start solving your supply chain problems.
Learn how Chain.io can help you achieve a connected, cost-optimized supply chain that drives real results.
Talk to Supply Chain ExpertsSee the Platform